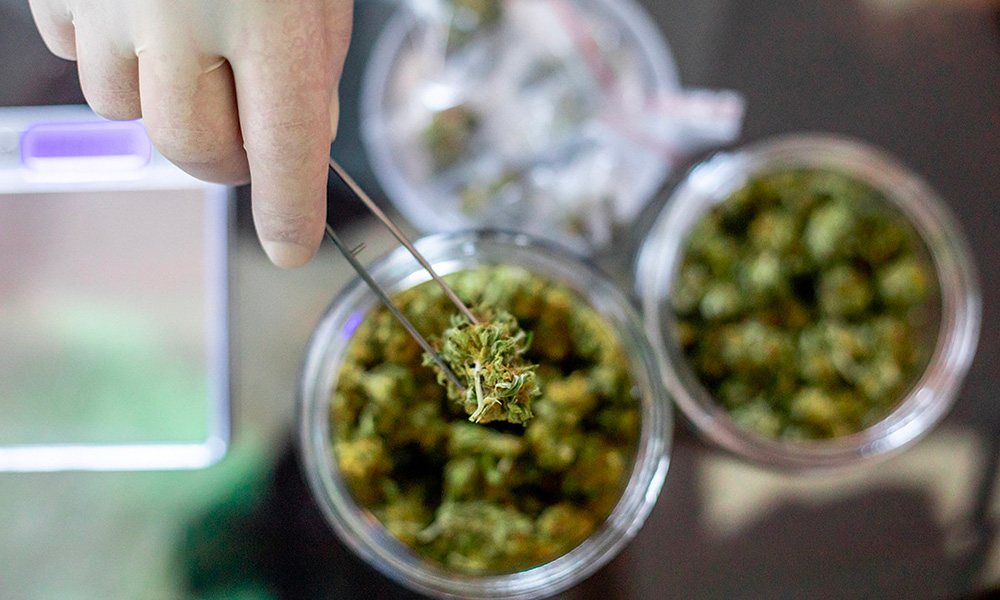
Q&A
George Terry of Rad Source Technologies on Cannabis Decontamination
Rad Source Vice President George Terry shares how the leading X-ray tech company moved into cannabis, and why its proprietary technology is so effective in decontaminating cannabis.
Meet George Terry, the dynamic Executive Vice President of Rad Source Technologies and the President of Rad Source NDT. He’s also a seasoned veteran in the realms of science and medical technology. Having honed his expertise through his time as a pharmacy analyst and an eight-year stint in orthopedics with the renowned Stryker, Terry’s five-year journey with Rad Source is just the tip of the iceberg.
In this exclusive interview, Terry delves into an intriguing intersection of his expertise, shedding light on the pivotal role of X-rays in the world of cannabis decontamination.
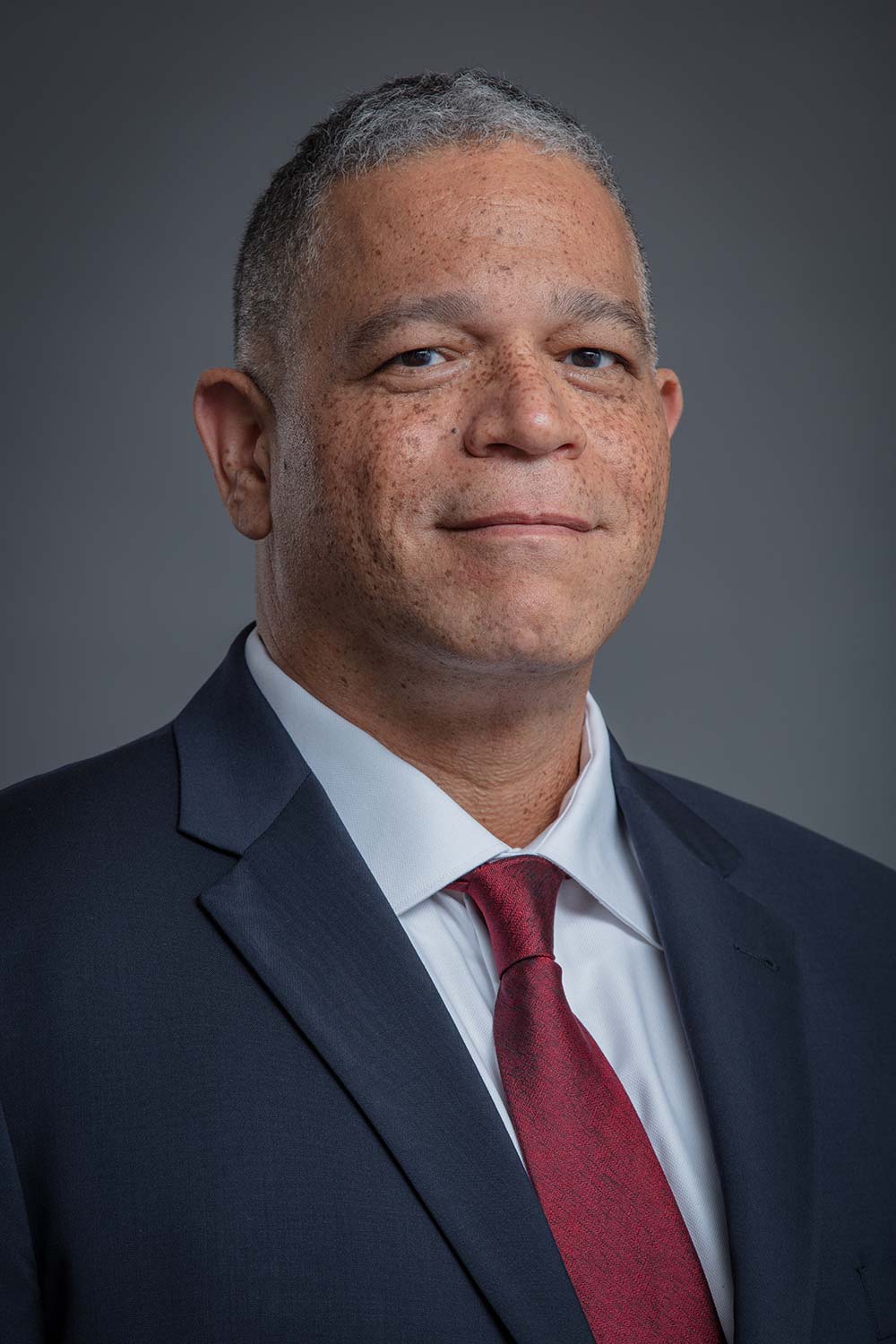
Cannabis Now: Tell us about Rad Source and its various ventures.
George Terry: We’re involved in cancer research, viral inactivation and sterile insect techniques. We’ve even delved into mosquito control using X-rays. Our manufacturing division, based in Lawrenceville, GA, is our pride and joy. We produce almost every component of our machines, ensuring top-notch quality control.
CN: How do Rad Source machines ensure safety from X-ray emissions?
GT: Our Quastar powdered devices adhere to the 21 CFR 1020.4 regulation pertaining to cabinet X-ray devices. When our cabinet is closed, no X-rays escape, ensuring safety without needing protective gear, like radiation suits.
CN: Rad Source is a pioneer in bridging X-ray technology with cannabis. Can you discuss the challenges and experiences in collaborating with cannabis cultivators and introducing this tech?
GT: It’s been a rewarding journey. Once we understood the industry and growers’ needs, it set our direction. Our technology inactivates the DNA in microbes, destroying them at a DNA level, ensuring the product passes state-mandated microbial testing while retaining the flower’s integrity. This approach is similar to methods used on products like chicken, strawberries and spices. However, instead of using a high-powered gamma level, we utilize a gentler approach, akin to shifting from a 1000-watt light bulb to a 25-watt one.
CN: What led Rad Source to enter the cannabis industry?
GT: Rad Source has been a world leader in blood irradiation for over a decade. The company was at the forefront when the shift began from nuclear isotopes to X-ray. Our primary focus was on blood irradiation using X-rays to prevent graft-versus-host disease. When I joined, we had a few clients in the cannabis sector and I’ve helped expedite our engagement in this industry.
CN: Can you delve deeper into the technology behind these machines?
GT: The Rad Source 3400 Series deactivates T lymphocytes inside white blood cells to prevent transfusion-associated graft-versus-host disease. It’s a crucial procedure for safe blood transfusion. The Quastar X-ray technology is non-nuclear and its capabilities extend beyond medical applications. For cannabis, our machines deactivate DNA inside microbes, inactivating them and ensuring the product is safe and uncontaminated.
CN: For those less familiar with the technology, can you discuss the types of microbial contaminants found in cannabis that your machines address?
GT: The primary microbial threats are Aspergillus, total yeast, mold, E. coli and Salmonella. Our RS 420 Series addresses all these and other bile-tolerant gram-negative bacteria.
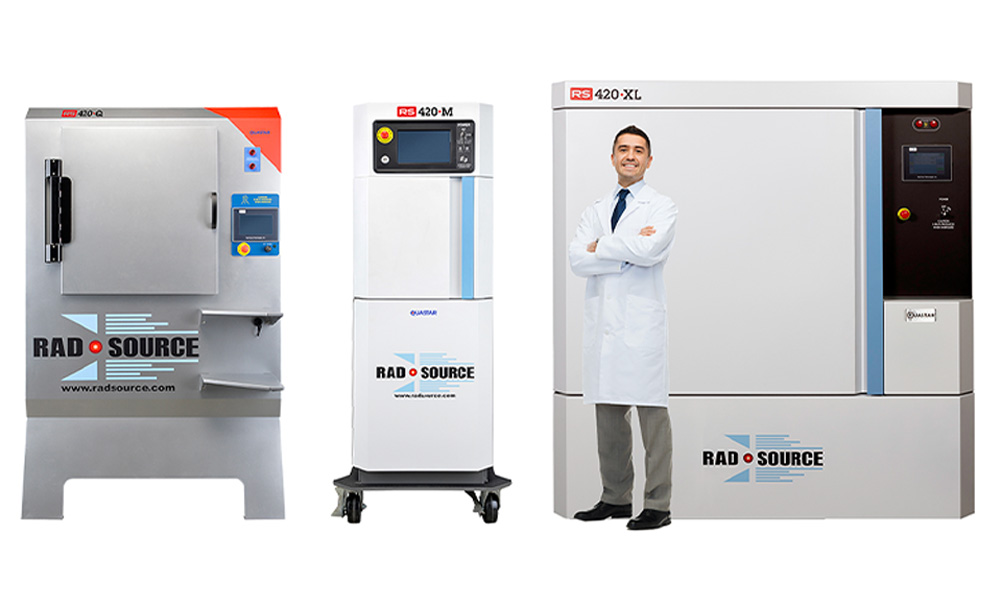
CN: Tell us about Quastar and its significance.
GT: Quastar represents the pinnacle of X-ray emitter technology for biological irradiation. This patented technology enhances the X-ray market for biological sciences by producing a more robust, consistent and energy-efficient photon field, leading to improved treatment uniformity, quicker processing and minimized adverse effects on targets.
Radiation is a part of our daily lives, from the sun’s rays to radio waves. The fear of the term ‘radiation’ is often unfounded. As we move down the electromagnetic spectrum, wavelengths shrink. This property allows X-rays, which have wavelengths the size of atoms, to penetrate deeper than, say, UV rays.
CN: Do you feel the cannabis industry is held to higher regulatory standards than others?
GT: I’ve actually been blasted for my position on this. I firmly believe that cannabis growers face stricter standards than many other sectors. There’s a push for “clean-grown” cannabis, which is a commendable goal. Yet, this standard isn’t applied to other industries like poultry or produce uniformly. Regulatory standards, especially in states like California, Colorado and Michigan, are robust and prioritize public safety.
CN: Speaking on a global scale, how do you perceive the cannabis market and its regulations?
GT: Cannabis is increasingly recognized as medicine. This recognition has expanded globally, from the US to Canada, the Netherlands and other parts of Europe. The regulatory frameworks in these regions vary, but the key goal is public safety. While there are variances, regulators worldwide emphasize keeping consumers safe and ensuring product quality.
CN: How do cannabis regulations compare domestically vs. internationally?
GT: Both domestic and international regulators prioritize consumer safety; they are the first line of defense against potential harms. However, standards might differ. For instance, while some states in the US test for Aspergillus, others don’t. Internationally, the standards can be quite stringent. Europe, for example, focuses on “medical-grade cannabis,” which has its unique requirements.
CN: Are there any Rad Source units in Europe?
GT: Yes, we currently have a unit in the Netherlands and are planning for another ten units for the European market by the end of this year. We also have units in South America and recently deployed ten units in Canada.
CN: Given the high cost of your units, how do micro growers find a solution for potential problems without investing in the quarter-million-dollar machine?
GT: We offer machines of various sizes, but I understand the concern. Depending on state regulations, we’ve seen “toll processing.” For instance, in Michigan, caregivers would bring their products to a toll facility with one of our units. The facility would charge a rate, like $100 a pound, to process the cannabis. This service is available in Colorado, Michigan and Massachusetts. We aim to expand this offering, but regulations can sometimes be challenging.
CN: What upcoming innovations or technologies is Rad Source introducing to the market?
GT: We’re striving to bridge a market gap we’ve identified. We’re in the final stages of developing a device designed for the 5 to 20-pound market segment. Additionally, our proprietary Quastar technology sets us apart. Traditional X-ray technology hasn’t evolved much in over a century. Quastar, on the other hand, offers a high-quality beam of photons in a uniform pattern, which aids in the decontamination process. It’s a game-changer in ensuring product safety without compromising its quality.
CN: What’s the current stance on cannabis in your company’s revenue stream?
GT: Cannabis is fast emerging in our revenue structure. Interestingly, as the international blood market saw some declines, cannabis bridged that gap for us. The growth in this vertical is often linked to state regulations. As more states introduce strict safety guidelines, the demand for our technology surges. For instance, after Colorado introduced Secret Shopper programs, we saw a rush of suppliers seeking our services to ensure compliance.
CN: What’s Rad Source’s footprint in Michigan and Colorado?
GT: In Michigan, we have over 40 sites. A standout statistic from Colorado’s Cannabis Control revealed that 90% of the flower in the state is processed through one of our units. This overwhelming majority underscores our technology’s effectiveness and its rising dominance over older methods.
CN: Do you have any final thoughts on the decontamination of cannabis?
GT: The stigma surrounding cannabis decontamination is misplaced. Every grower aims to produce clean products. However, like all-natural products, cannabis can be exposed to contaminants. Having reliable methods to decontaminate these products is essential while meeting state-set safety standards.
