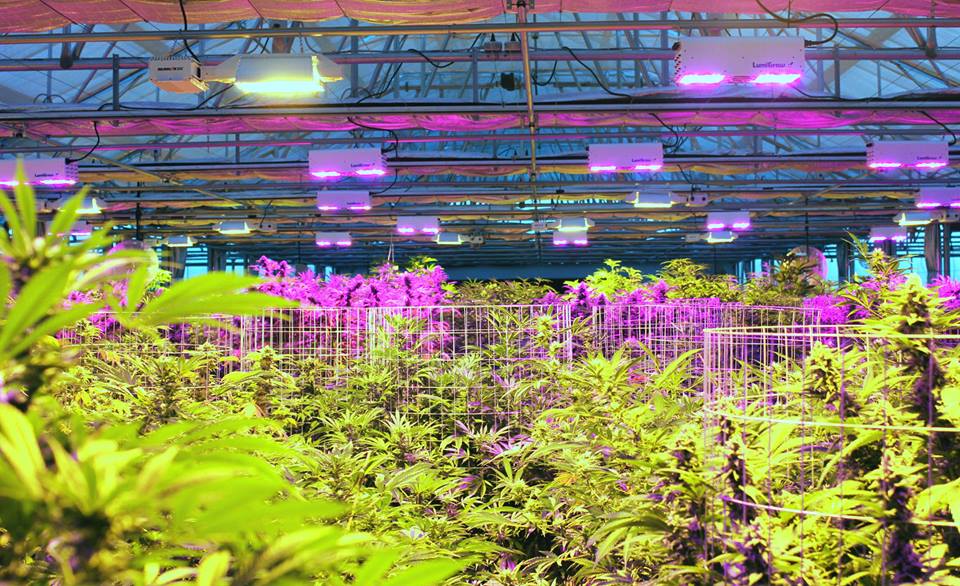
Cultivation
Cannabis Cultivators Look Towards Energy Efficiency
It would be inaccurate and disrespectful to countless prohibition era pioneers to say the current cannabis industry sprouted up overnight.
Its literal and figurative roots were planted decades ago, when the idea of square corporations pushing legal trees wasn’t even the stuff of comedy sketches yet.
Still, in just a few short years, the legal cannabis industry has experienced rapid expansion. And as more states adopt legalization or decriminalization measures, cultivators are rushing to expand their operations to meet skyrocketing public demand.
But Ryan Bonelli, president of Cultivation Suppliers, says most of that growth isn’t sustainable and much of it is “grossly inefficient.” He doesn’t blame growers though, he says it’s just another industry hangover from the days of total prohibition.
“From about 1999 to 2009 there was an explosion in cannabis cultivation, the majority of which was done residentially,” he said. “It was a non-regulatory environment… and because growers could be forced to tear down their setup and move their garden at any moment, these early systems lacked long-term commercial viability.”
When the market came to scale in 2014 with Washington and Colorado legalizing cannabis for recreational use, Bonelli says many growers kept using the same equipment they did for their residential grows. He says one excellent example of this is air-cooled lighting.
“Air-cooled lights were designed for bedrooms – small lighting arrays that had anywhere from two to four grow lights – and it was made to mitigate the heat effect on height potential. So if your ceiling is short and your plants are tall, you can grow closer to the lights since you can’t raise them,” he said. “But I’ve been down there and seen grows with 200 air-cooled lights. All they’re doing is moving heat from one end of the room to the other and there’s really no advantage.”
Bonelli says a cultivator needs to keep three things in mind when planning operations: cost per gram, grams per watt and price per gram.
And when it comes to the how behind the watt, that’s where Ryan Knight, vice president of Cultivation Efficiency Systems (CES), steps in.
CES is an energy and analytics company specializing in energy regulation compliance for businesses, which means they help clients find the cheapest, most efficient energy solutions. Bonelli says this makes Knight an invaluable resource for CES clients.
For his own part, Knight says he’s strictly an “energy guy,” but he’s passionate about energy efficiency and thinks cultivators will be too – once they realize the impact it has on their bottom line.
“Clearly in the cost per gram figure there’s a percentage of that going to energy expenses, and our research puts that number anywhere between 25 and 50 percent,” he said. “That means even if it’s only 25 percent and we cut it in half, we just saved you 12.5 percent.”
In California, cultivators can expect to pay roughly 14 cents per kilowatt hour. But with one of CES’ onsite power generation systems, that cost can be reduced to about 6 cents.
Knight says in addition to positively impacting profits, improved energy efficiency will help bolster the professional image of California’s burgeoning legal industry.
“If we want to have any chance of creating a great name for our state’s new industry, we’re going to need sustainable energy practices,” he said.
One of the primary solutions CES offers its clients is on-site power generation using natural gas. Knight says purchasing power off the grid involves transferring electricity over miles, so the end user is only getting a fraction of the energy used to generate and deliver their power.
“But if we use on-site natural gas and utilize the waste heat for cooling and environmental control, then we’re using around 90 to 100 percent of the fuel burned for a process,” he said. “It varies state by state, but here in California we can do that for about half the cost of purchasing power from the grid,” adding that CO2 is one of the byproducts of the system and can be utilized in the grow.
And systems like those offered by CES also provide analytics, giving cultivators the ability to pin down the power cost of pushing a given strain.
Obviously, such advanced systems represent a substantial capital expense, but both Knight and Bonelli agree the energy savings pay for themselves within two to four years. And moving forward, the level of efficiency and environmental control offered by these types of systems is likely to become the industry standard.
Do you grow cannabis? Tell us your grow stories!
